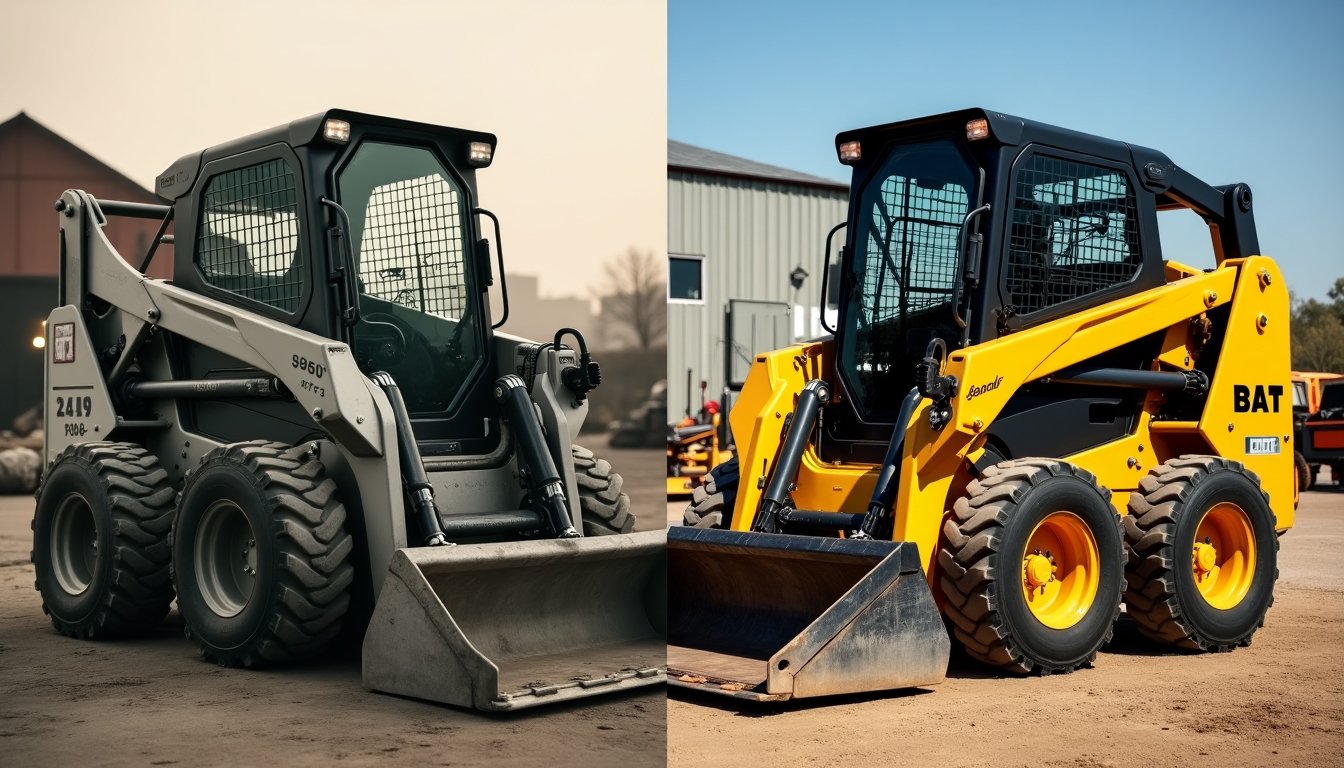
The skid steer loader story began in an unexpected place - a small Minnesota turkey barn in 1957. A simple solution to clean poultry manure grew into construction's most versatile equipment.
Skid steer capabilities have evolved dramatically in the last six decades. These compact powerhouses have progressed from simple material handlers to sophisticated machines with automated features. Modern skid steers handle diverse tasks from construction and landscaping to specialized industrial work. The progression from that first loader to today's advanced models reflects remarkable engineering achievements and innovation.
This piece explores the evolution of skid steer technology. We'll look at breakthrough developments in attachment systems, performance capabilities, operator comfort, and future-ready features that revolutionize the industry.
Pioneering the Compact Equipment Revolution
The story starts in the workshops of Rothsay, Minnesota. Brothers Cyril and Louis Keller ran a small machinist-blacksmith shop in the 1950s. Their innovative mindset would revolutionize the construction equipment industry with what became the first skid steer loader.
The Original Problem-Solving Vision
Local turkey farmer Eddie Velo came to the Keller brothers with a unique challenge in 1956. He just needed a machine light enough to work on the second floor of his turkey barn. The machine also had to maneuver around upright poles spaced just eight feet apart. The brothers' solution to this challenge would become the foundations of modern skid steer solutions.
Early Market Challenges
Success didn't come right away. The Keller brothers faced major funding obstacles and just needed USD 250,000 for a manufacturing facility. Local banks provided only partial funding. The city of Fergus Falls offered help but wanted controlling interest in the patent - a deal the brothers rejected.
Les Melroe of Melroe Manufacturing Company spotted their invention and everything changed. Melroe saw a successful demonstration at the 1958 Minnesota State Fair. He offered to manufacture the loader on a royalty basis and brought the Keller brothers on board to refine the design.
Industry Adoption Milestones
The industry's rise has been remarkable:
- Melroe launched their first self-propelled loader, the M60, in late 1958
- The groundbreaking M400 became the world's first true four-wheel skid-steer loader by 1960
- The iconic M440 Melroe Bobcat arrived in 1962 and introduced the now-famous Bobcat brand name
The market has grown exponentially, reaching USD 9.7 billion in 2023. A turkey farmer's simple problem led to equipment that revolutionized construction, agriculture, and industrial sectors.
Modern machines still follow the original design principles, and that's the sort of thing I love about this story. The simple concept of differential steering and compact maneuverability remains central to today's skid steer solutions, even with sophisticated hydraulic systems and advanced control mechanisms.
Versatility Through Attachment Innovation
Skid steer capabilities have grown remarkably through attachment technology advances that have changed how these machines serve multiple industries. Bobcat's introduction of the Universal Skid Steer Quick Attach (SSQA) system in the 1970s became a defining moment in attachment innovation.
Evolution of Attachment Systems
Attachment systems have progressed from basic mechanical connections to advanced hydraulic interfaces. A standardized mounting system now lets operators switch between attachments without leaving the cab 4. Construction sites have become more efficient with reduced downtime.
Task-Specific Tool Development
Specialized attachments have grown to meet industry needs of all types. Modern skid steer solutions now include:
- Advanced mulchers with high-flow hydraulic systems that clear dense vegetation
- Precision grading attachments with laser-guided technology
- Specialized concrete handling tools for construction applications
- Heavy-duty demolition attachments built for durability
Modern hydraulic systems have adapted to these demanding applications. They offer flow rates from 15-25 GPM for standard operations and 26-40 GPM for high-flow applications .
Universal Compatibility Standards
The industry's shift toward universal compatibility standards marks an exciting development. The Society of Automotive Engineers (SAE) released complete specifications for the "Universal Attachment Mount" in June 2000. The International Organization for Standardization (ISO) later adopted this as standard 24410 in 2005. Different manufacturers' attachments now combine smoothly with various skid steer models thanks to this standardization.
The compatibility framework relies on three key factors: hydraulic flow requirements, weight capacity limitations, and mounting plate specifications. Manufacturers can now develop specialized tools while maintaining broad compatibility across different machine models.
Skid steer solutions have evolved from simple material handlers into versatile construction powerhouses. Modern attachment systems handle operating capacities from 1,250 lbs to 4,200 lbs. Operators can now tackle demanding tasks in industries of all types.
Performance Optimization Breakthroughs
Recent performance breakthroughs in skid steer solutions show remarkable advances that reshape jobsite capabilities. These breakthroughs bring major improvements in power, precision, and versatility.
Load Capacity Advancements
New models demonstrate dramatic improvements in lifting capabilities. The Cat 250's rated operating capacity has increased by 21%, while the Cat 260 shows a 17% improvement over previous models 7. Equipment operators can now handle heavier materials confidently and efficiently.
Key performance improvements include:
- Increased tilt breakout force - up to 36% higher in new models
- Improved lift breakout force - showing 26% improvement in latest designs
- Greater lift heights - reaching up to 146 inches in larger models
Maneuverability Improvements
Modern skid steer solutions feature impressive stability improvements. The latest design's engine compartment places both engine and cooling systems lower in the frame. This groundbreaking engineering gives operators better confidence when they handle heavy loads during various work cycles.
Hydraulic System Breakthroughs
The hydraulic system's development has revolutionized performance. Modern systems now offer:
Feature | Specification |
Standard Flow | 23 GPM @ 3,500 psi |
High Flow | 34-36.6 GPM @ 3,500 psi |
Super Flow |
42 GPM @ 4,061 psi |
New models feature radiators and oil coolers that are 30% larger than previous generations. Dual-direction bucket positioning and automatic ride control make operations more efficient.
These performance breakthroughs deliver smarter operations beyond raw power. Advanced electronic controls allow operators to adjust hydraulic flow precisely based on specific attachment needs and working conditions.
These improvements create real-life benefits in productivity. Operators report better cycle times and improved material handling capabilities. The combination of increased power and refined control systems helps tackle demanding tasks with greater precision than before.
Operator Experience Transformation
The change in operator experience with modern skid steer solutions stands as one of the major improvements in compact equipment design. These changes are reshaping operator comfort and productivity.
Control System Development
Traditional mechanical controls have moved to sophisticated electronic systems. The latest models now feature electro-hydraulic controls that provide unmatched precision and customization. Modern cabs have dual-level suspension systems that reshape operator control. The seat-mounted joysticks move with the suspension seat to improve comfort during operation.
The development of control systems has:
- Selectable Joystick Controls (SJC) with switchable patterns
- Automatic ride control to reduce material spillage
- Integrated attachment controls through advanced displays
Comfort and Visibility Improvements
The dramatic improvements in cab design are remarkable. The latest models offer 20% more interior space than their competitors. This creates a more comfortable environment for extended operation. The cab experience now has:
Feature | Benefit |
Pressurized Cab | Keeps dust out and maintains climate control |
Front Door Seal | Increases pressurization effectiveness |
Adjustable Suspension Seat | Accommodates different operator sizes |
Visibility improvements stand out with new models that feature a 34% increase in viewable area through the top window. Advanced camera systems now provide wide-angle views of traditionally hard-to-see areas.
Training and Certification Advances
Operator training approaches have transformed. Modern certification programs combine traditional classroom instruction with hands-on experience and sophisticated simulation technology. The latest training systems now have:
- Interactive online learning modules
- Virtual reality-based operation scenarios
- Live performance monitoring and feedback
The industry accepts complete training programs that require 16 hours of hands-on equipment operation training. These programs cover simple operations to advanced attachment handling. Operators get proper preparation for modern skid steer operation's complexities.
The way these improvements work together creates a more productive and safer operating environment. Better controls, improved visibility, and advanced training protocols have substantially reduced operator fatigue while boosting overall efficiency.
Future-Ready Features and Capabilities
The next generation of skid steer solutions brings groundbreaking developments that reshape how these machines work and interact with their surroundings. Compact equipment's future unfolds right before us with innovations that would have seemed impossible just a few years ago.
Autonomous Operation Development
Remarkable advances in autonomous capabilities continue to emerge. Bobcat leads this revolution with their RogueX concept machine. Their innovative platform explores autonomous operation without an operator station and enables work in areas where human presence might be restricted or dangerous . Advanced sensors and LIDAR technology help the system direct and complete tasks with remarkable precision.
Remote operation serves as a crucial step toward complete autonomy. Modern systems now let operators control machines from distances up to 400 meters away 7. This advancement makes hazardous work environments substantially safer without compromising productivity.
Alternative Power Solutions
Electric power solutions represent an exciting development in the field. Here are the latest specifications:
Feature | Specification |
Battery Capacity | 60.5-kWh lithium-ion |
Operating Time | Up to 8 hours per charge |
Charging Time | Approximately 10 hours |
Torque Output | 3x greater than diesel equivalents |
Electric models have reshaped jobsite operations. They eliminate emissions and cut operational costs by up to 70% compared to diesel counterparts. These machines run on just one quart of eco-friendly coolant, unlike diesel-hydraulic models that need nearly 60 gallons of fluids .
Next-Generation Safety Systems
Safety systems have made impressive strides. Modern skid steer solutions now feature:
- AI-driven pedestrian recognition technology that can reduce vehicle/pedestrian accidents by two-thirds
- Advanced radar collision warning systems with automated slowdown capabilities
- Smart attachment recognition that automatically configures control patterns for specific tools
Telematics systems now provide critical machine information remotely. Operators can monitor machine health and identify potential maintenance issues early. Remote access to vital machine data enables proactive maintenance scheduling and better uptime management.
These developments create a more efficient, safer, and sustainable working environment. Smart attachments communicate directly with the machine's control systems and automatically adjust operational parameters to achieve optimal performance.
Conclusion
Skid steer solutions started in a Minnesota turkey barn, and they've sure come a long way since then. Today's machines combine smart technology with practical features that make them vital for construction, agriculture, and industrial work.
These machines have made incredible strides. Standardized attachment systems boost their flexibility, while advanced hydraulics tackle tough jobs with pinpoint accuracy. User-friendly controls and better comfort features have made these machines more efficient than ever before.
The road ahead looks bright. Manufacturers now accept new ideas like electric power, self-driving capabilities, and AI safety systems. This points to a future where skid steers will get smarter and safer while staying true to what makes them great - their adaptability.
The skid steer's story teaches us something valuable. A simple fix for one problem can turn into a game-changing tool that reshapes whole industries. These machines keep getting more advanced, but their core purpose stays the same: they help operators work faster and take on tough jobs with confidence.
References
- https://en.wikipedia.org/wiki/Skid-steer_loader
- https://www.skidsteerhistory.com/How%20it%20began.htm
- https://www.gminsights.com/industry-analysis/skid-steer-loaders-market
- https://www.skidsteersolutions.com/inside-the-cab-skid-steer-solutions/are-skid-steer-attachments-universal-a-comprehensive-guide/?srsltid=AfmBOoqpkJcdi_-z8YCqMrO6gnTo3M_Rnkolsnua9r6aR0fAfrFLL_fz
- https://www.skidsteerforum.com/threads/here-is-the-universal-attachment-specification.6803/
- https://dozr.com/blog/skid-steer
- https://www.cat.com/en_US/news/machine-press-releases/caterpillar-launches-eight-new-next-generation-cat-skid-steer-loaders-and-compact-track-loaders-with-more-power-performance-and-comfort.html
- https://www.bobcat.com/na/en/equipment/loaders/m3-series/operator-comfort